Designing Against a Pandemic
In the midst of the COVID-19 crisis, as medical supplies dwindle, hospitals internationally are looking to designers for new medical materials.
Images from Inside Weather
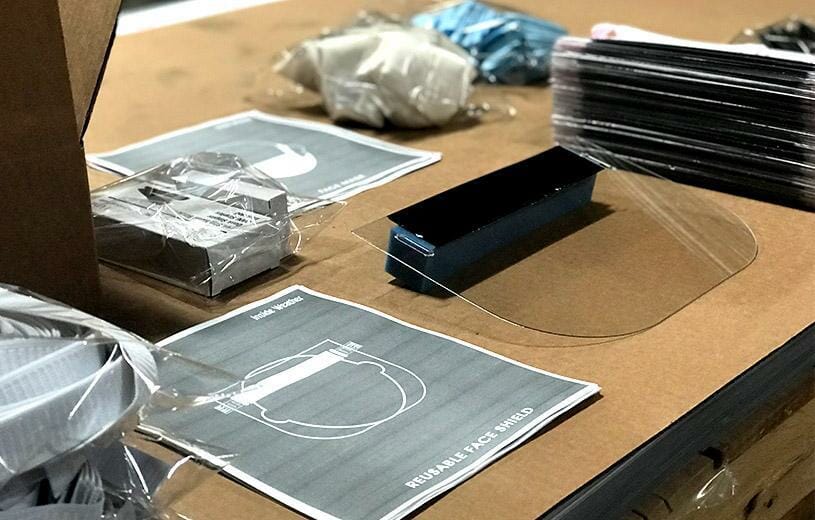
By Sabaat Kareem
Essential equipment for patients and doctors such as face shields, testing swabs, and ventilators are speedily running out of stock. Designers, however, have been quick and generous in their response; for example, those who specialize in 3-D printing have been working around the clock to provide hospitals with enough supplies to continue treating patients.
COVID-19 is a highly contagious respiratory illness with flu-like symptoms. The testing and treating of COVID have proven to require more medical equipment than is readily available or readily manufacturable. Countries, regardless of what they manufacture, are vehemently trying to import supplies, but, still, many hospitals are left without the necessary stock. Every person being tested for the virus is tested with a disposable swab, and because the virus targets the lungs, patients with the virus may need a ventilator to help them breathe. Additionally, in order to treat patients, doctors need to wear protective gear like masks or face shields. Supplies are extremely limited and hospitals are amidst a catastrophe of running out of materials. While regular manufacturers are trying to fill the gaps in supplies they are unable to produce enough. With fast action and innovation, designers have combated this issue by adjusting their practices to contribute to the production of equipment. From small businesses to million dollar companies, designers have taken on the community responsibility of using their creativity to aid the world-wide emergency.
Here at CoDesign, we’ve partnered with UShield, which has fielded over 34,800 requests since going live last week. They stamp PPE masks out, which cuts down on production time and do not require any assembly. Also, we’re connecting designers in our network to Boston-area hospitals to rapidly create CPAP helmets, which are simple hoods to aid in breathing, that are not as invasive as ventilators, and are simpler to manufacture.
In Liverpool, New York one of such small businesses has managed to 3-D print over 10,000 face shields for their county. Isaac Budman and Stephanie Keefe run Budmen Industries, a company that sells custom 3-D printers. Hearing that a virus testing site was opening nearby, the two designed a prototype for fast and comfortable shields and were asked by the county to send in 300 units for use. Their operation prints plastic visors that wrap around the head. They then cut and attach a clear shield from a polyethylene sheet which can be discarded or disinfected after use.
Inside Weather, a furniture company, has an online, open source hub for creating face masks, face shields, and containment boxes.
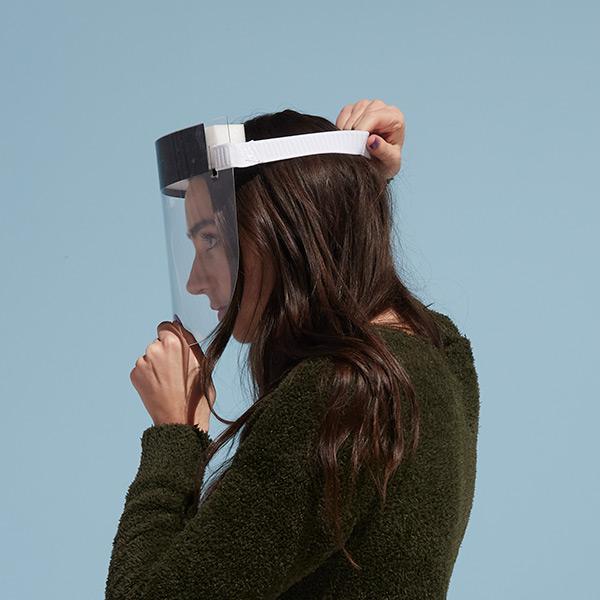
On an international scale, the company known for its vacuum cleaners and dryers, Dyson, has designed an original ventilator called the CoVent. The CoVent was designed to prioritize rapid production and the “specific needs” of COVID-19 patients. After a conversation between the UK Prime Minister Boris Johnson and James Dyson in mid March, this new ventilator was designed in the lightning speed time of ten days and should have 15,000 units ready in early April.
Until the new ventilator is ready, however, the traditional ventilator will have to do. Ventilator parts are becoming especially scarce in every part of the world because the valve of the machine must be replaced between every patient. For this reason, valves for ventilators are especially sought after and their limitation in quantity have already led city leaders to warn their populations that without enough valves sick people who are wholly savable will die. Christian Fracassi, CEO of Isinnova in Italy, developed a replacement for the ventilator valve in only a few days. Due to the extremely emergent situation the testing period for the valve was waived and the Venturi valve went into action immediately. The valves have been helping the local hospital ever since completely free of charge. Since the valve was rushed into operation without standard testing practices, the valve cannot be used outside of Italy.
The Massachusetts based 3-D printing company, Formlabs, has not only been printing testing swabs, face shields, and ventilator parts, but have been acting as a network to link their customers to medical centers in need. Anyone with a printer at their disposal can fill out a form online and Formblabs will connect them with a medical facility, and, reversely, a medical facility can also fill out a form and request to be linked to a printer. On their website they have included a thorough guide on how to safely print medical devices and have recorded their printing efforts in detail. Currently, they are printing much needed testing swabs and are in the testing stages of their ventilator tubes and masks. Formlabs’s effort is an incredible feat for the communication between medical professionals and designers during this sudden pandemic.
The ways in which designers and engineers have been swiftly adjusting to the current situation are broad and bountiful. Many other companies, groups, and individuals have put in the work to aid the impacts of COVID-19. What has become extremely clear during this time is the necessity of innovation, quick thinking, and spirit in times of strife. We are happy and proud to see how design has made this frightening period a bit more hopeful.